Text & Interview: Alec Coiro
Photos Courtesy of Toyine Sellers
Toyine Sellers weaves the sort of textiles that make a house a home. They contain enough of the trace of the hand that wove them to feel personal, to feel like a material you can connect with. Be it in the form of a rug or a pillow or upholstery, Sellers’ work is both carefully and beautifully fabricated; it is created with an eye for color and patterns that produce a subdued vibrancy that helps bring a room quietly to life. Sellers shares that her unique perspective on color comes from her peripatetic childhood and all the cultural influences she absorbed as a result of it.
As cosmopolitan as her upbringing may have been, though, Sellers seems to have resisted contemporary, computerized approaches to weaving. She opts instead to approach the process in a more intimate way on looms dating all the way back to 1960s, and the results are apparent in the warmth of textiles she produces.
Of course, Sellers puts this better than we can in our interview. She goes into depth on her background, her techniques, and even gives us a sneak peak into the future, including her plans to expand into the realm of velvet and mohair.
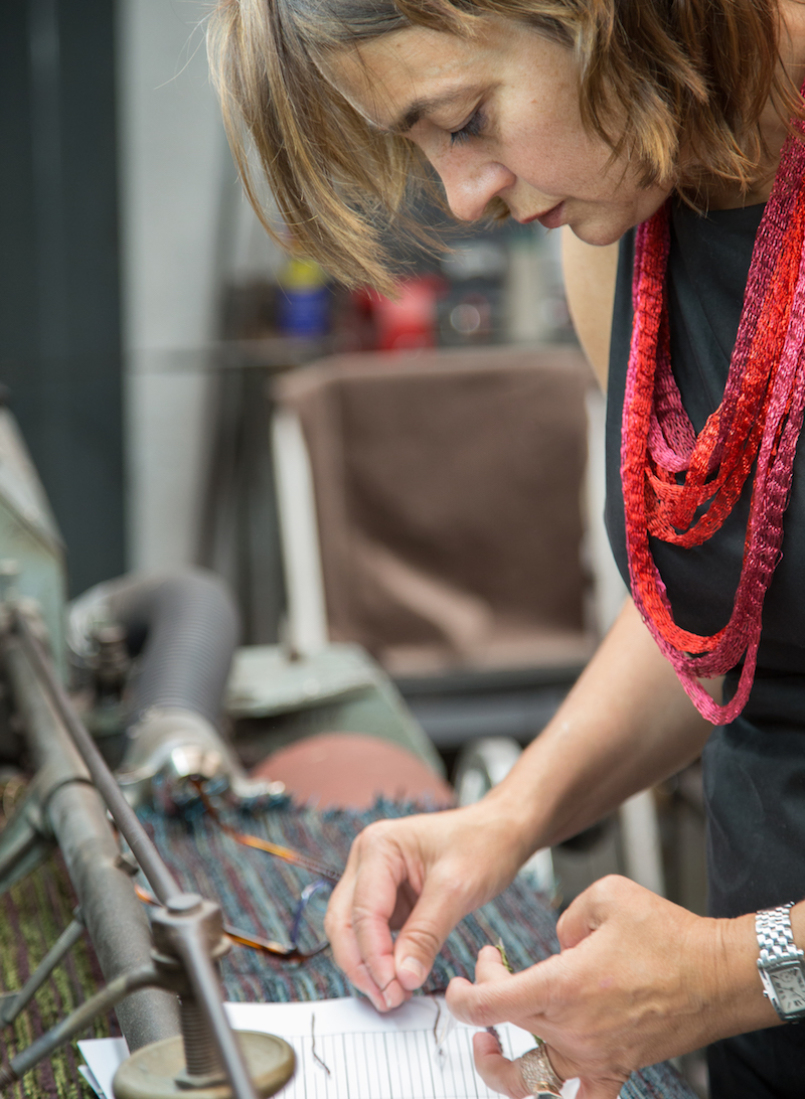
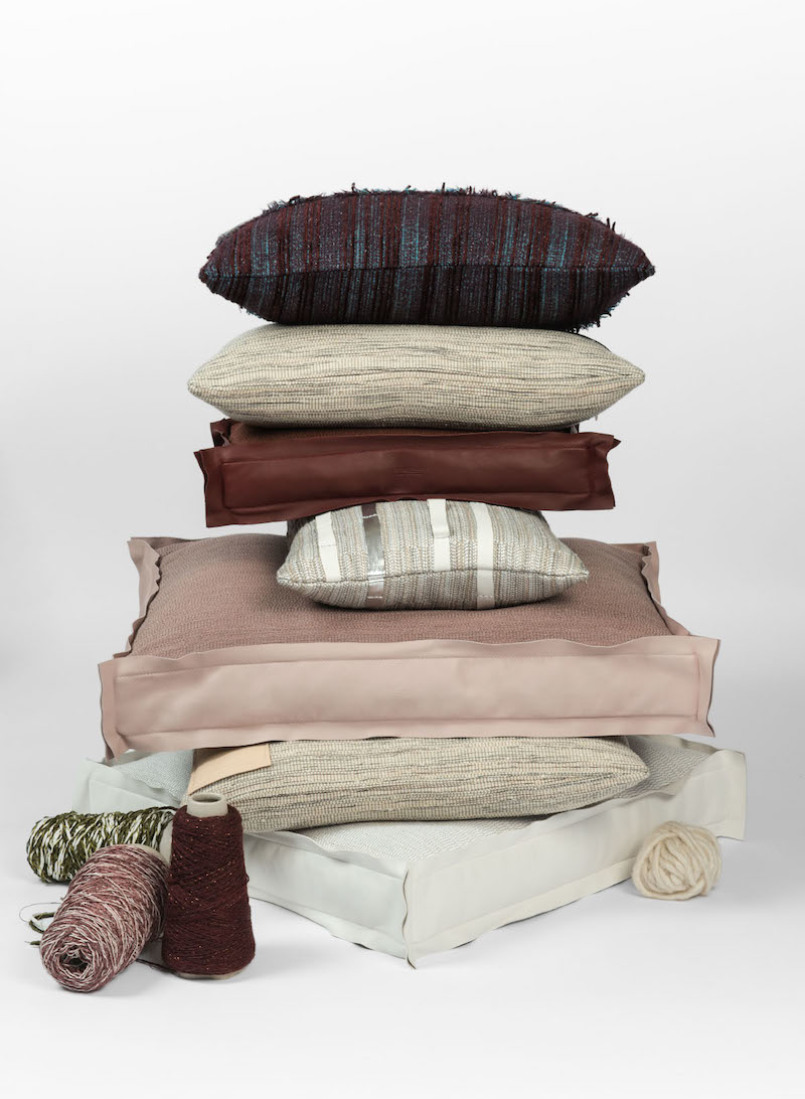
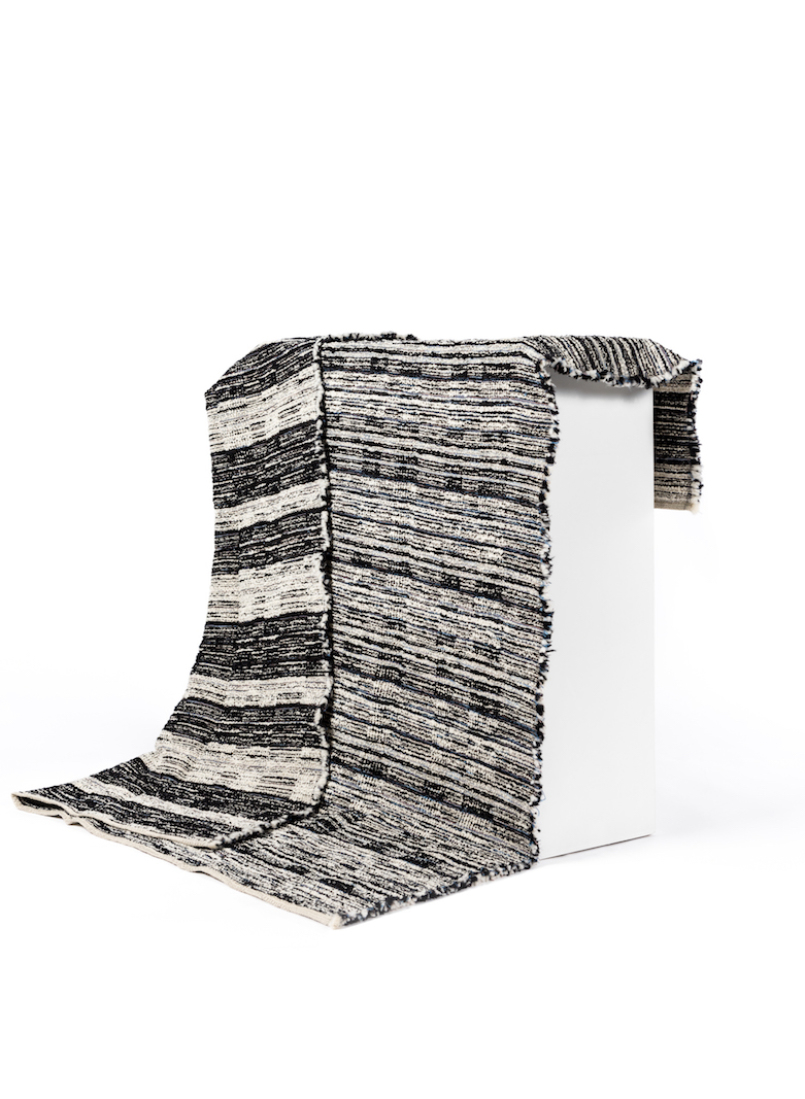
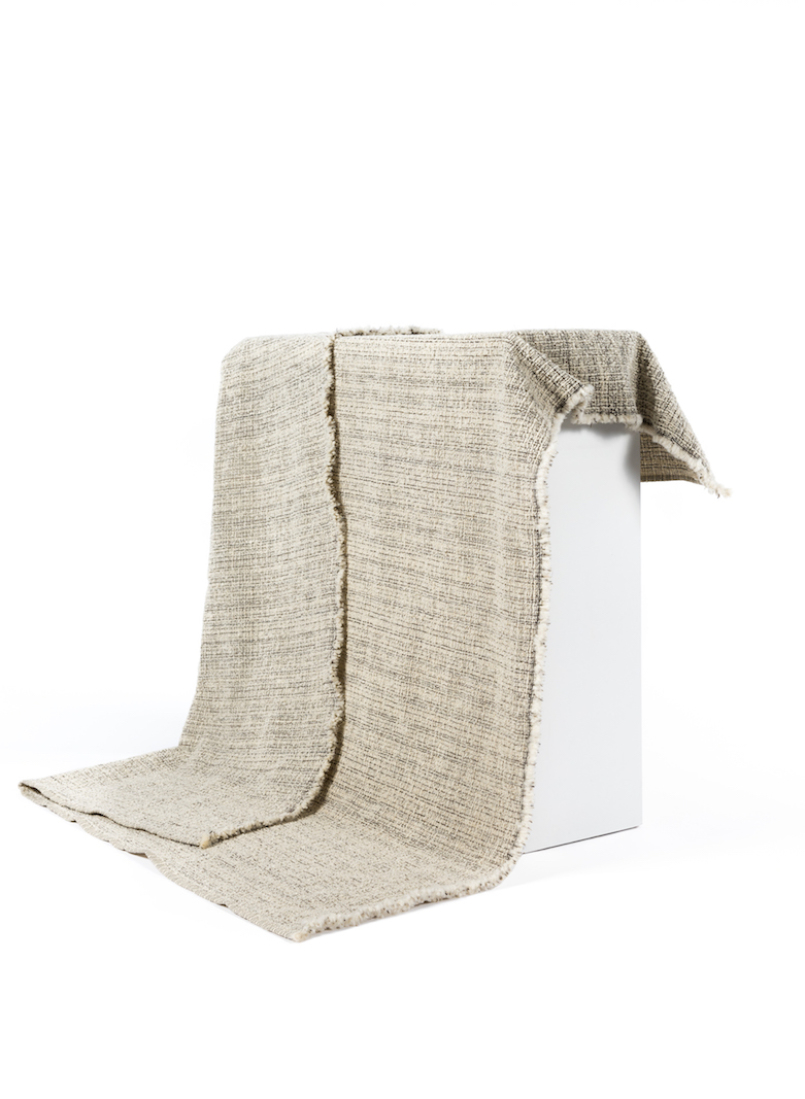
You have such an international background; how has that influenced the way you think about design?
As a child, I was infused by the “flavors” of the places I lived: the language, the climate, the people, the music, the art and the colors. These stayed with me with me with each move but were covered by tastes of the next place. Desperate to fit in, I would quickly adapt, adopt, embrace and absorb the new environment. I never did fully fit in, no matter how I tried, I was a mille-feuille of nationalities.
From all those layers of flavors and the memories, come the unique color combinations and textures I create. Now I am happy to stand apart even stand out through them.
I understand that you employ old world crafting techniques; can you take us through the details of what that entails?
I think the labor intensive manner in which we work and the length of time it takes us to produce something on our traditional looms, could be termed “old world crafting techniques”.
What we do to create a fabric can also be compared with what a chef does when he creates an amazing meal. If we are successful, both of us produce something delicious, beautiful and unique. There is considerable preparation work, which nobody sees, for both of us.
Every fabric we create has a recipe. Here, we list the ingredients and the quantities used. We note what must be blended together, called retordage (sorry I learned to weave in French so I do not know the English word), the process where we twist the yarns together. When we are working with leather, we must cut the hides into laniers or thongs, before being able weave them.
Once at the loom, we put the yarns in place and select the right carton (a sheet of plastic with holes in it, apparently the first computer program). This carton tells the loom the order in which to place the yarns and the pattern to weave them in. We adjust loom for the specific fabric, making sure we have the right density of the material, as we can weave most fabrics in curtain or upholstery weight. We always have one weaver per loom, as when mixing many different types of yarns into one fabric as I like, their different tensile strengths and thicknesses can make weaving complicated. The Weaver’s presence ensures the quality and is there to manage yarns which break or leather thongs which must be turned over. The end result is a beautiful material, with the necessary attention to detail, colour and quality.
In a less traditional weaving house with modern looms: the cartons are computerized, they have 1 weaver supervising 10 looms and their goal is to produce a minimum of 100 meters per loom, per day.
Our average weaving speed of 1-5 meters per hour, per weaver. Our textile looms date from the 60’s, though we recently bought a “new” one from the 80’s. We have two special velvet looms, also from the 60’s, and 3 hand looms for the rugs. One of these is “classé”, an antique that the French authorities monitor.
On a related note, I’m curious how you first came to the trade and learned to weave?
I was responsible for developing fabrics for the interiors of Louis Vuitton, Chanel, and other retail brands when I worked for Peter Marino. It was new to me; most interior designers are not trained for this! The first time, Peter handed me a photo and said make a fabric from this I had no idea what to do! I eventually figured it out and thanks to him, I discovered an amazing world of incredibly passionate, talented and devoted weaving artist.
It was only later, once I’d left Peter that I actually tried my hand at weaving. With no training, I did many things wrong, but that ended up becoming part of my look too. I like imperfection, I think it adds character and I often tell weavers I work with to “unlearn” what they were taught and allow mistakes to happen.
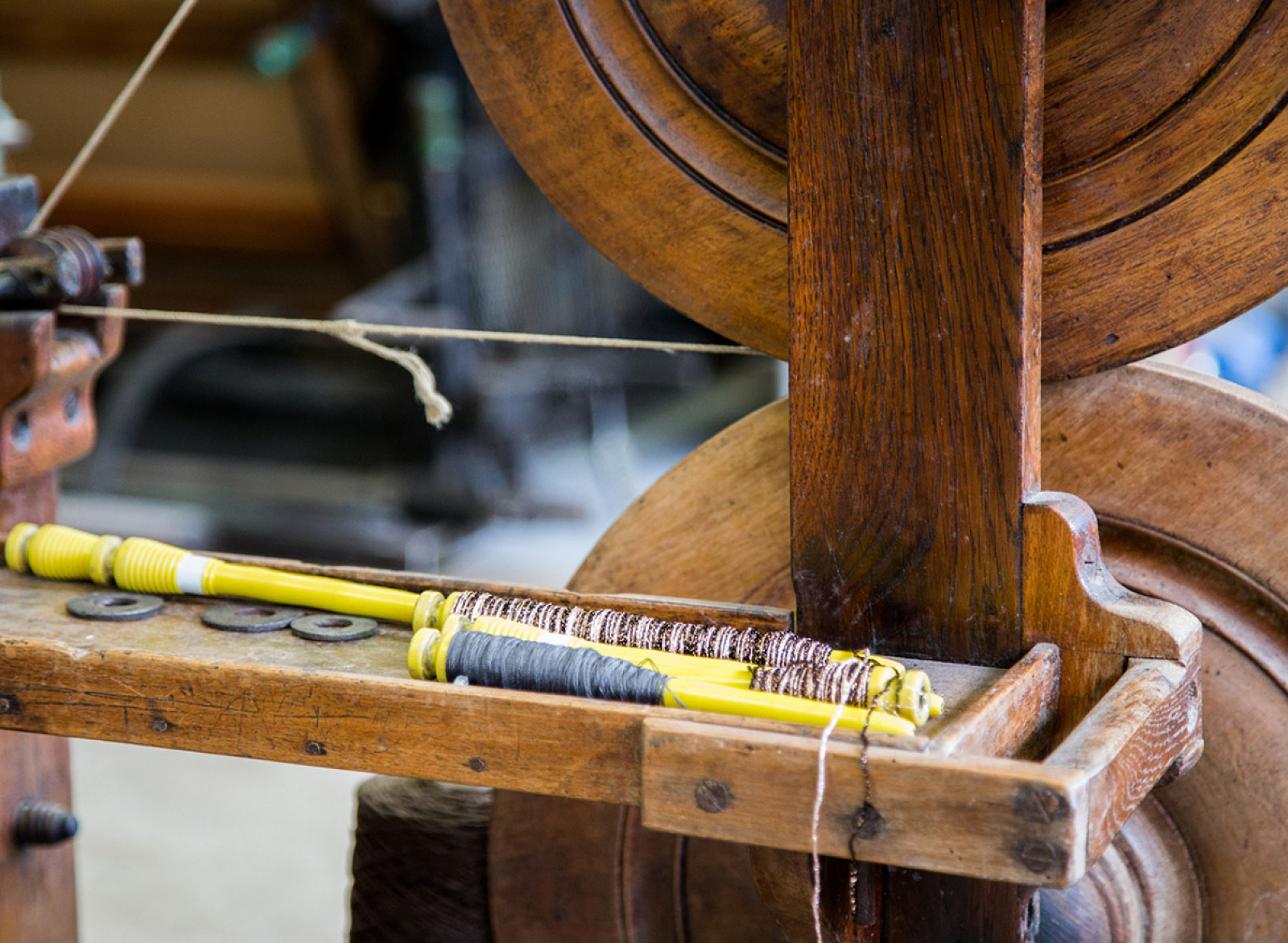
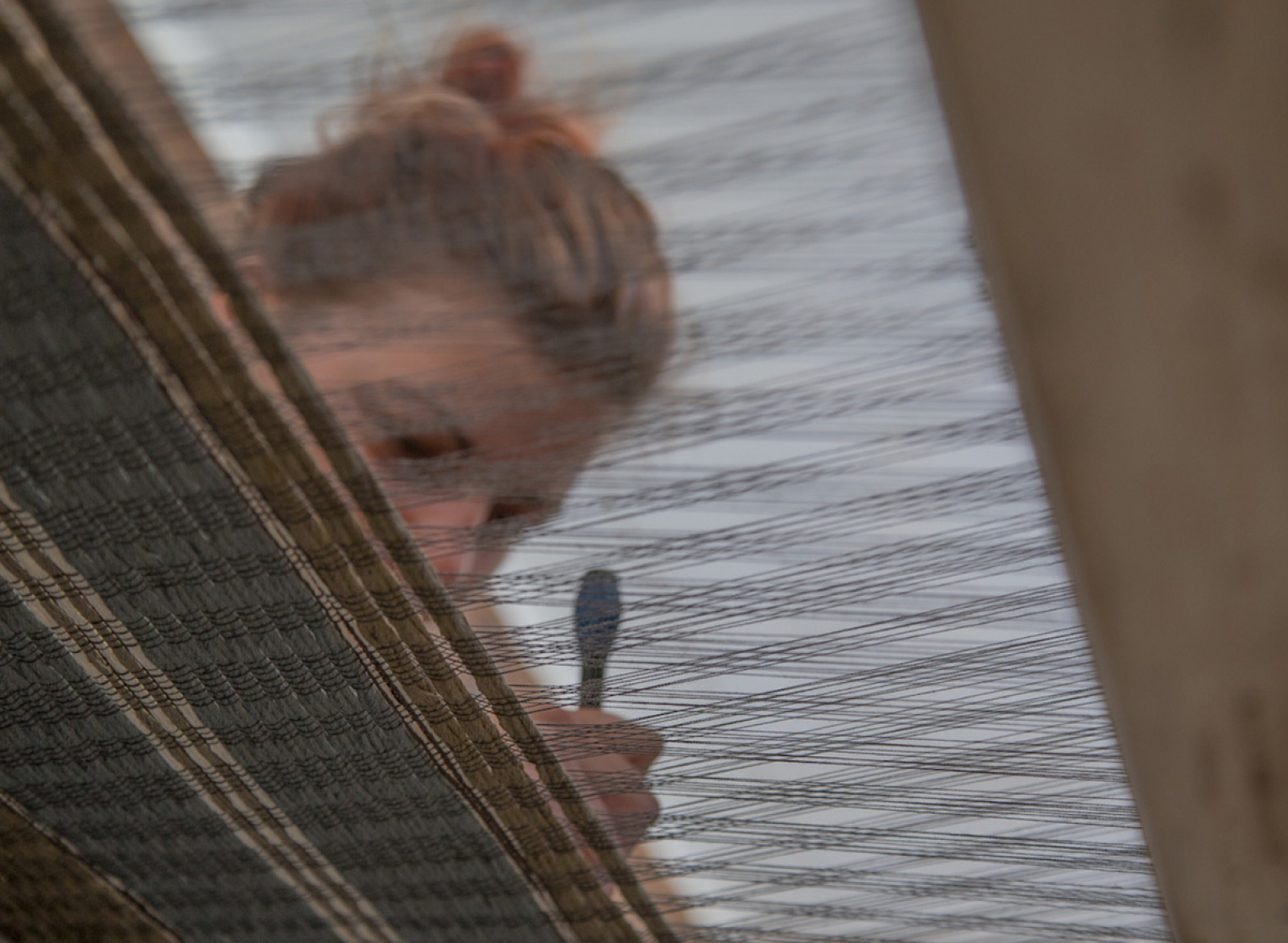
What we do to create a fabric can also be compared with what a chef does when he creates an amazing meal. If we are successful, both of us produce something delicious, beautiful and unique.
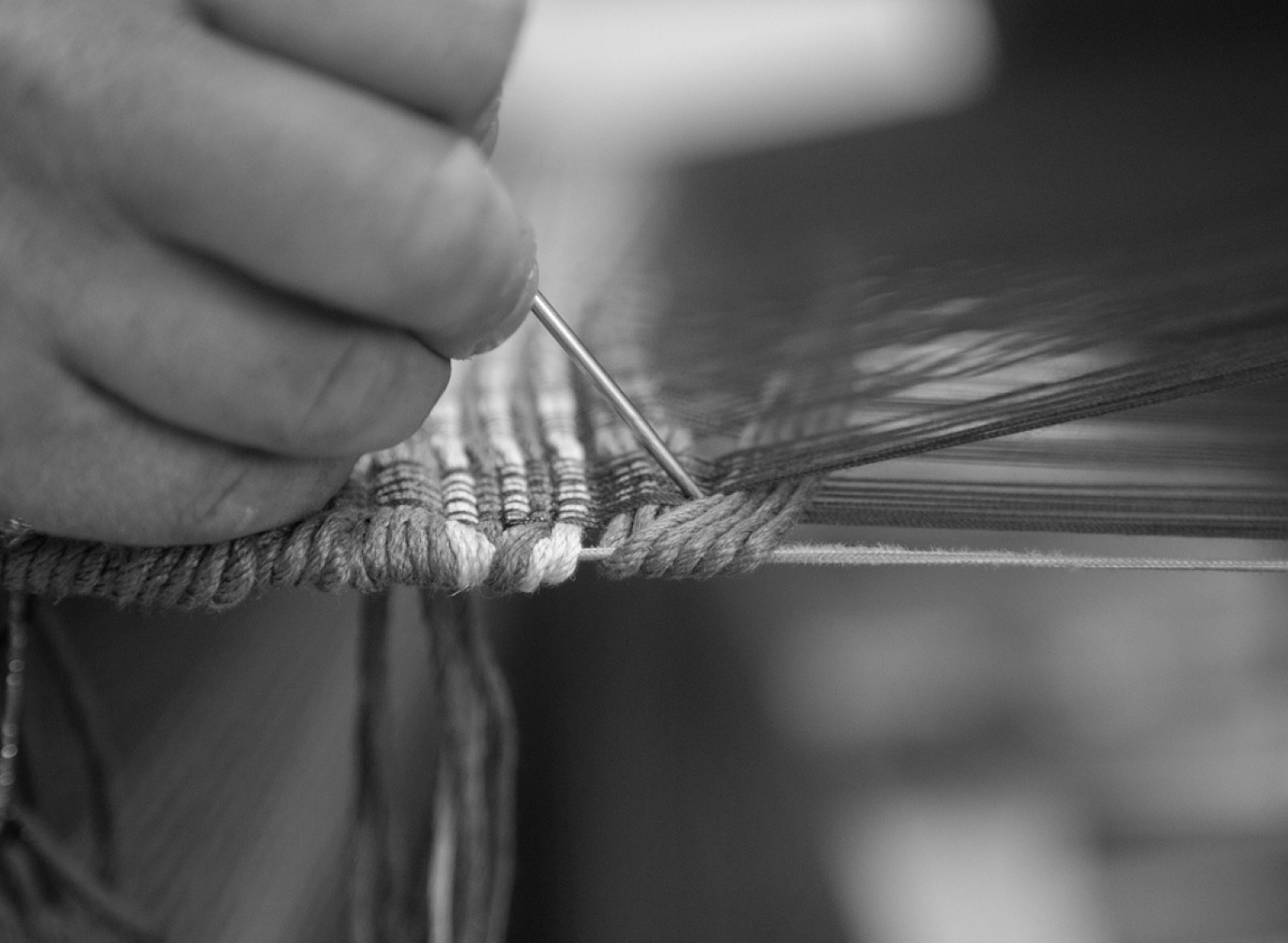
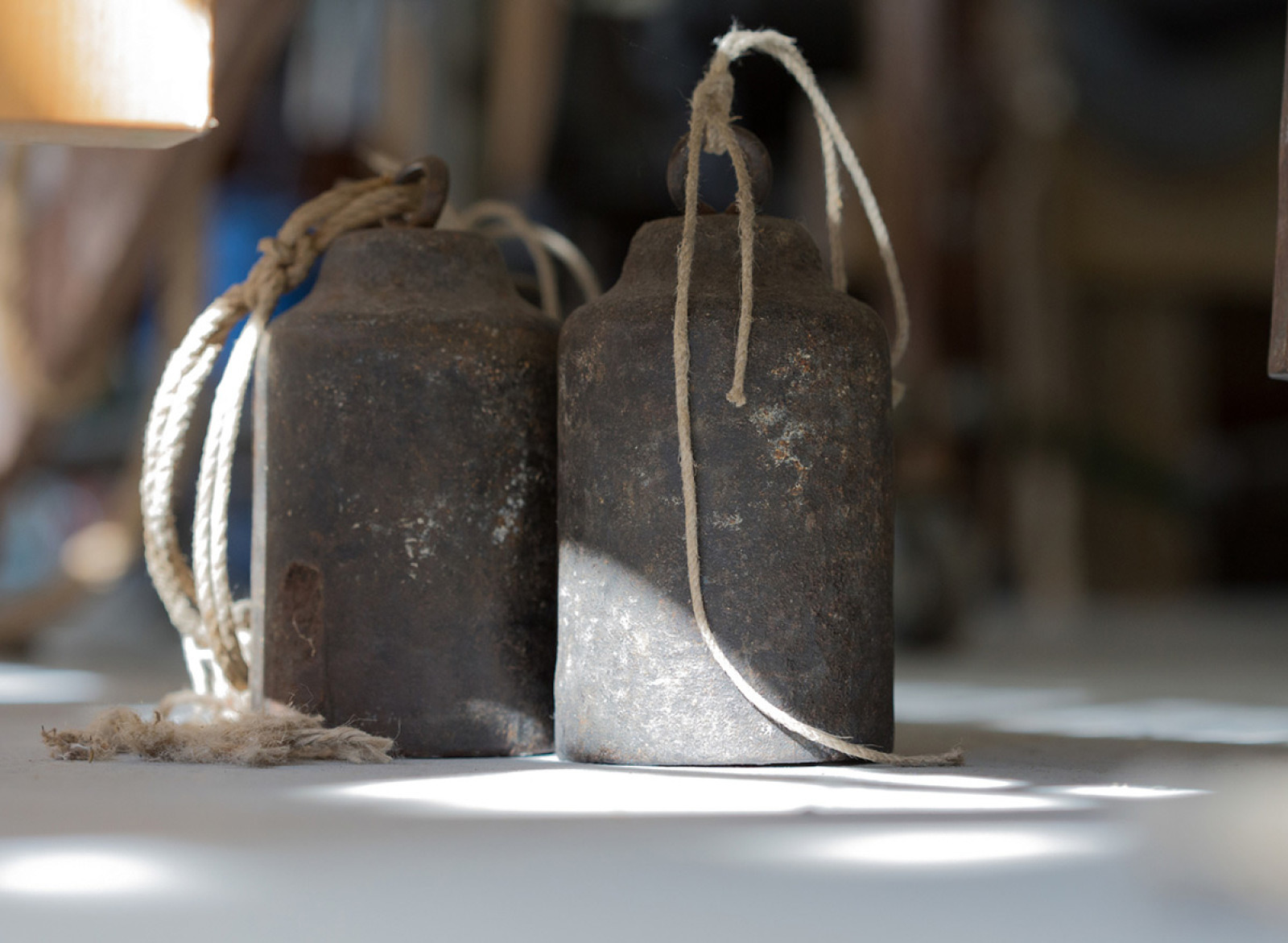
You have such an international background; how has that influenced the way you think about design?
As a child, I was infused by the “flavors” of the places I lived: the language, the climate, the people, the music, the art and the colors. These stayed with me with me with each move but were covered by tastes of the next place. Desperate to fit in, I would quickly adapt, adopt, embrace and absorb the new environment. I never did fully fit in, no matter how I tried, I was a mille-feuille of nationalities.
From all those layers of flavors and the memories, come the unique color combinations and textures I create. Now I am happy to stand apart even stand out through them.
I understand that you employ old world crafting techniques; can you take us through the details of what that entails?
I think the labor intensive manner in which we work and the length of time it takes us to produce something on our traditional looms, could be termed “old world crafting techniques”.
What we do to create a fabric can also be compared with what a chef does when he creates an amazing meal. If we are successful, both of us produce something delicious, beautiful and unique. There is considerable preparation work, which nobody sees, for both of us.
Every fabric we create has a recipe. Here, we list the ingredients and the quantities used. We note what must be blended together, called retordage (sorry I learned to weave in French so I do not know the English word), the process where we twist the yarns together. When we are working with leather, we must cut the hides into Laniers or thongs, before being able to weave them.
Once at the loom, we put the yarns in place and select the right carton (a sheet of plastic with holes in it, apparently the first computer program). This carton tells the loom the order in which to place the yarns and the pattern to weave them in. We adjust loom for the specific fabric, making sure we have the right density of the material, as we can weave most fabrics in curtain or upholstery weight. We always have one weaver per loom, as when mixing many different types of yarns into one fabric as I like, their different tensile strengths and thicknesses can make weaving complicated. The Weaver’s presence ensures the quality and is there to manage yarns which break or leather thongs which must be turned over. The end result is a beautiful material, with the necessary attention to detail, color, and quality.
In a less traditional weaving house with modern looms: the cartons are computerized, they have 1 weaver supervising 10 looms and their goal is to produce a minimum of 100 meters per loom, per day.
Our average weaving speed of 1-5 meters per hour, per weaver. Our textile looms date from the 60’s, though we recently bought a “new” one from the 80’s. We have two special velvet looms, also from the 60’s, and 3 hand looms for the rugs. One of these is “classé”, an antique that the French authorities monitor.
On a related note, I’m curious how you first came to the trade and learned to weave?
I was responsible for developing fabrics for the interiors of Louis Vuitton, Chanel, and other retail brands when I worked for Peter Marino. It was new to me; most interior designers are not trained for this! The first time, Peter handed me a photo and said make a fabric from this I had no idea what to do! I eventually figured it out and thanks to him, I discovered an amazing world of incredibly passionate, talented and devoted weaving artist.
It was only later, once I’d left Peter that I actually tried my hand at weaving. With no training, I did many things wrong, but that ended up becoming part of my look too. I like imperfection, it thinks it adds character and I often tell weavers I work with to “unlearn” what they were taught and allow mistakes to happen.
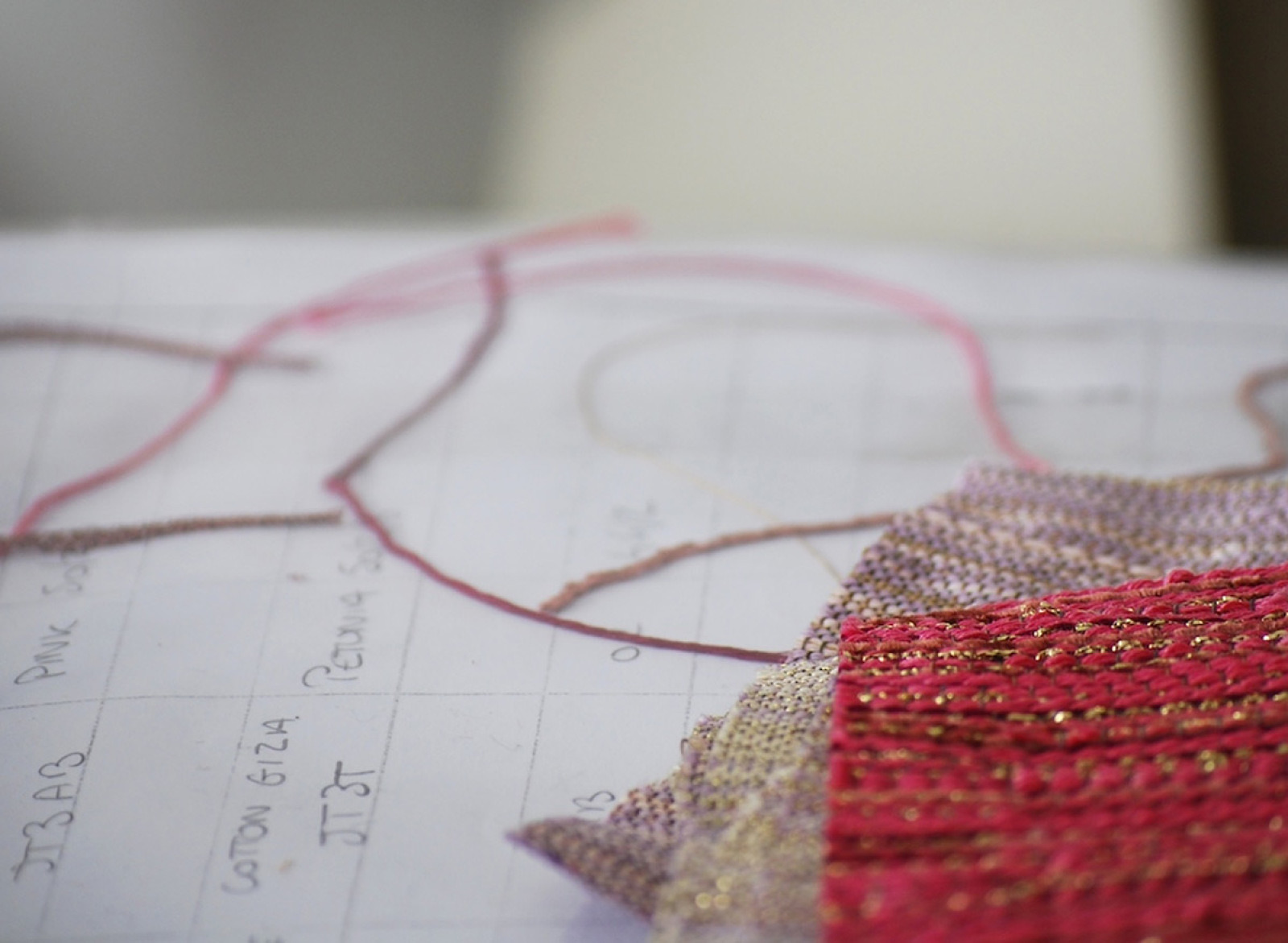
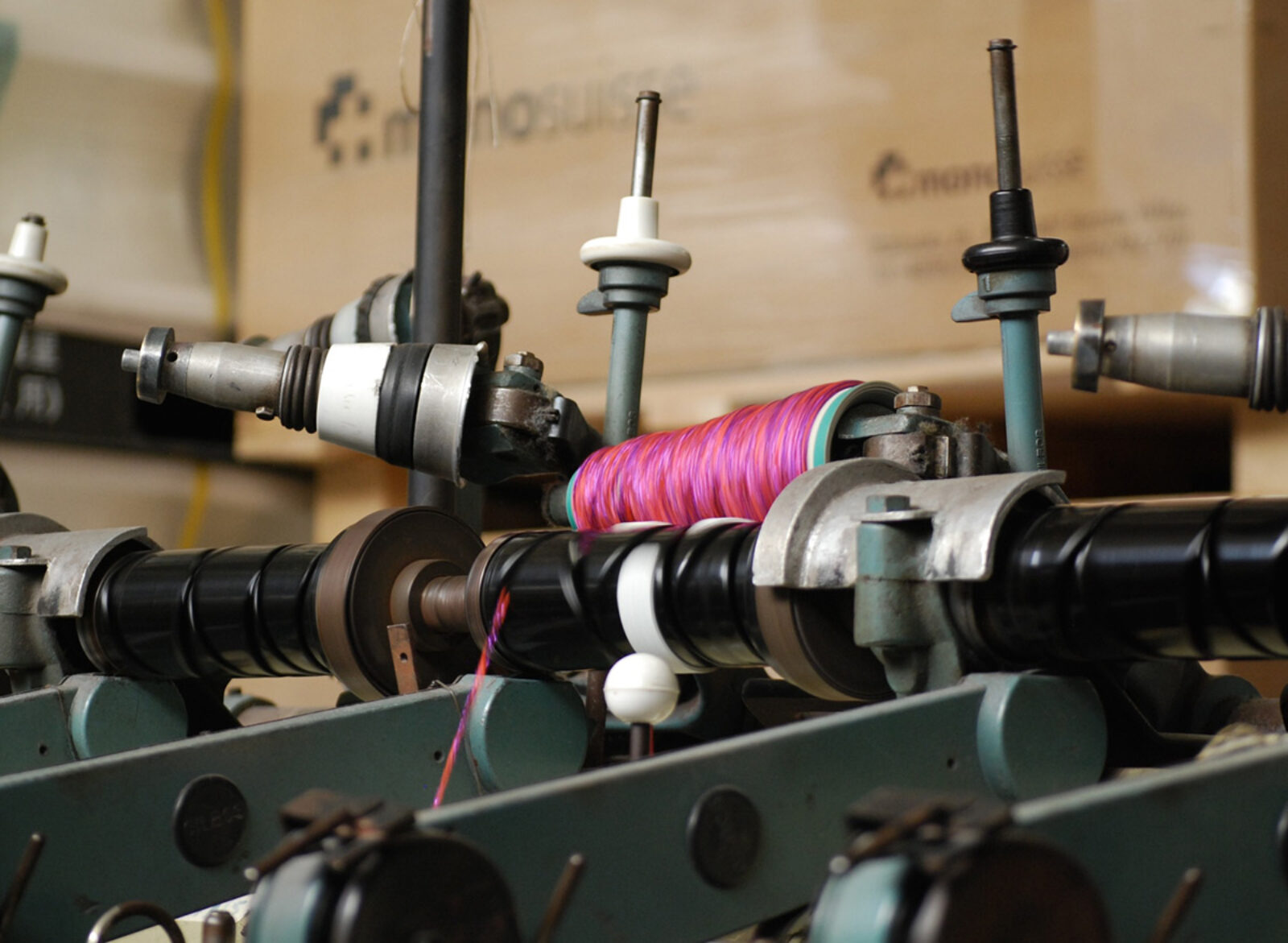
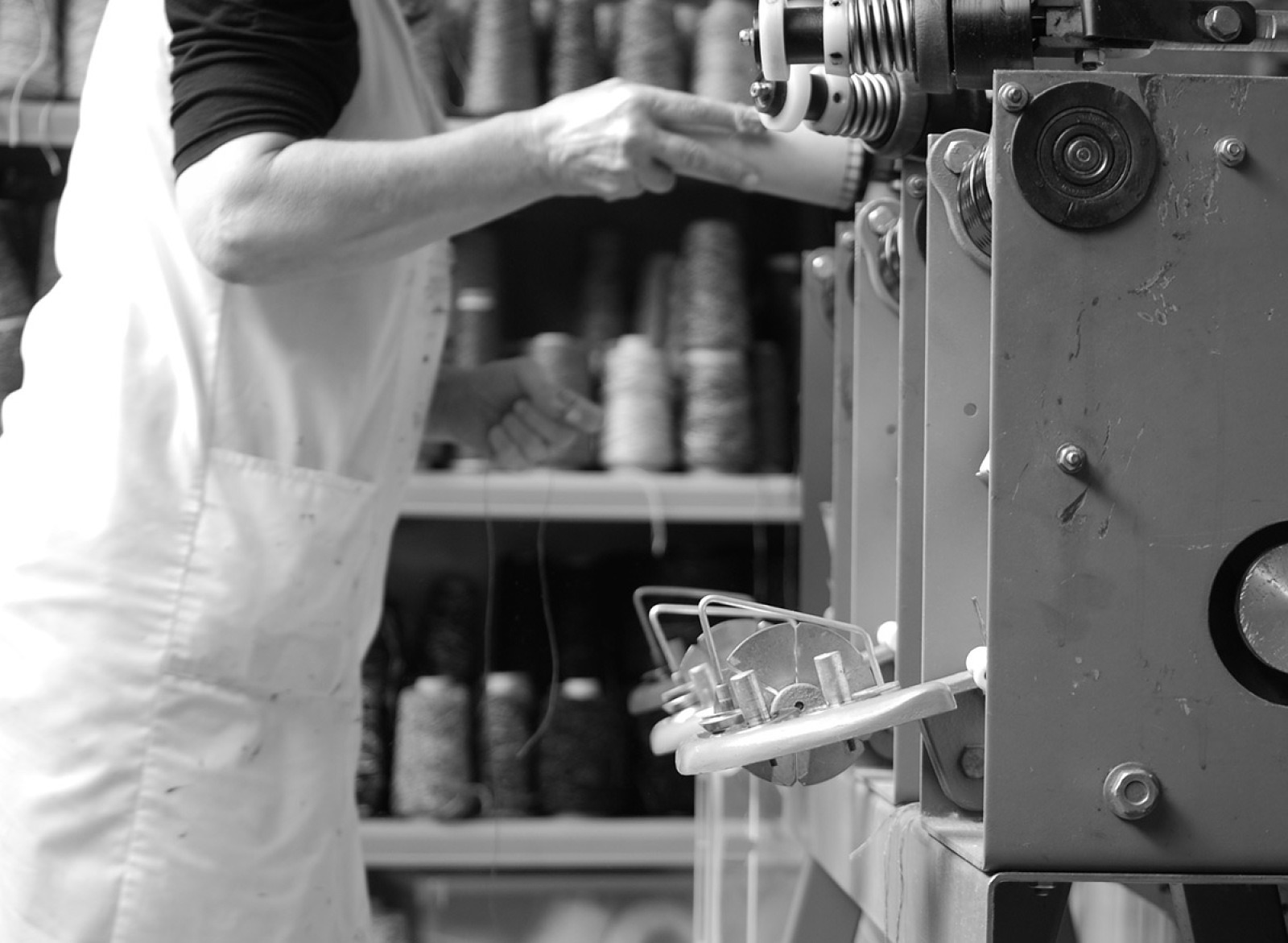

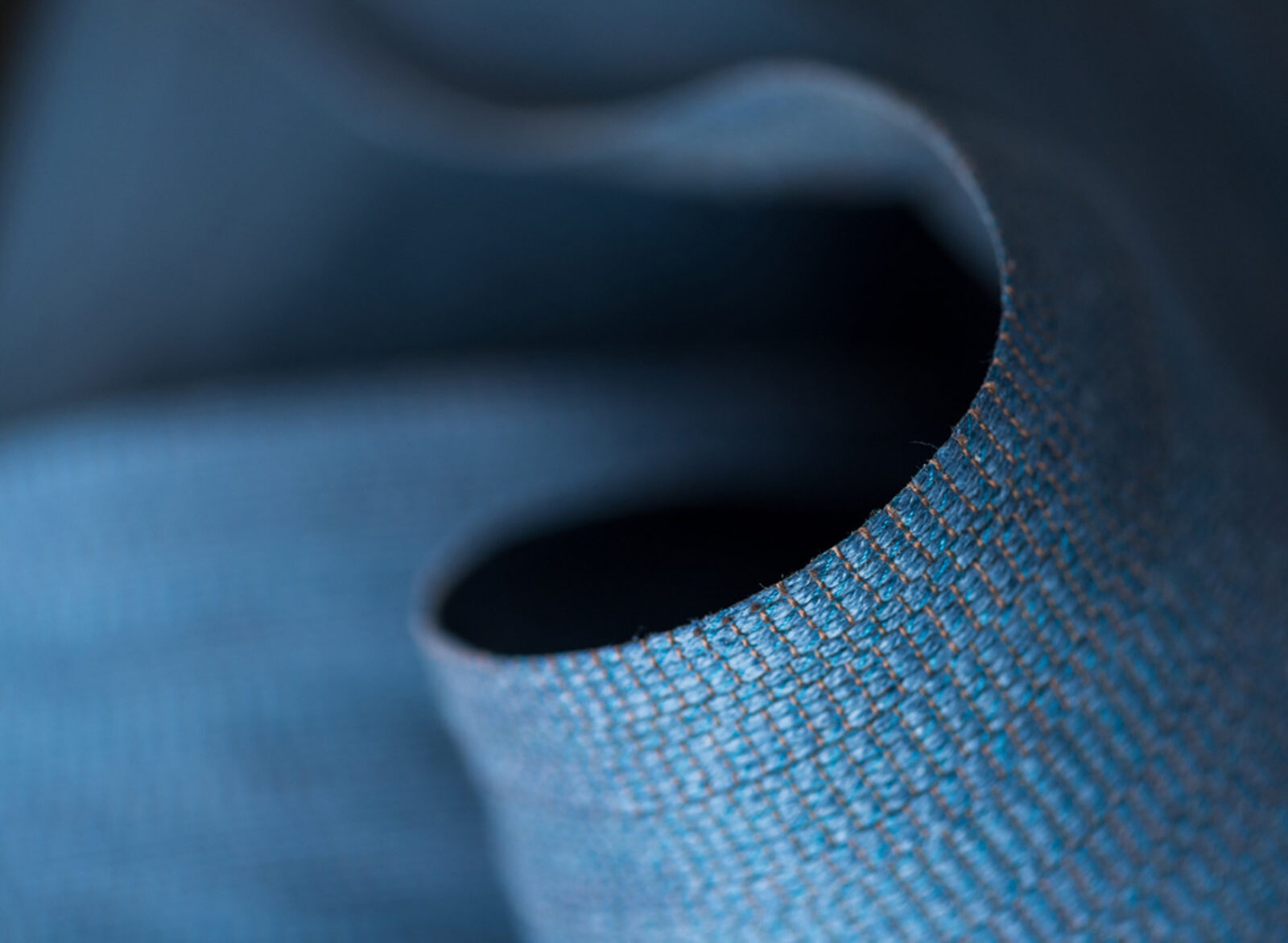